Raw Material
We use latest and modern gas carburizing process for case hardening and heat treatment of our products. Our quality control system and equipment ensure perfect geometrical and dimensional accuracies and our durability lies at our core with usage of high quality alloy steel.
Parameter |
Details |
At RITSUKA |
Chinese Product |
RITSUKA Advantage |
BOP (Bought Out Parts) |
Bearing |
BOP |
BOP |
We provide bearings from Taiwan maintaining OEM standards |
Raw Material |
Body |
20CrMo Steel grade Raw Material |
Substandard Steel Grade Raw Material |
High Strength & High Yield High Temperature resistant |
Bearing |
Taiwan Quality Bearing |
Chinese Bearing |
Our product offers exceptional mechanical properties like durability, comfort and longevity along with safe ride. |
Manufacturing
From the smallest to the most central element, each part is manufactured under stringent quality parameters that make us deliver the finest. We make every ride the smoothest by putting our products through rigorous checks before shipping.
Parameter |
Details |
At RITSUKA |
Chinese Product |
RITSUKA Advantage |
Manufacturing |
Machining |
CNC machining centre |
Semi-Automated or Manual |
By using fully automated CNC machines, we offer min. Tolerance level products with negligible rejection at final stage. |
Design centre, Tool room and R&D facilities |
Inhouse Design centre, tool room and R&D centre |
Not available with normal chinese factories |
RITSUKA has an extra ordinary aptitude in developing customized formulations for Steel products. For Moulded products, the company has in-house tool room with integrated facilities for mould design & mould manufacturing enabling quick lead time to customers. |
Moulding |
Automated moulding process |
Manual Moulding process |
Automated moulding results in Relatively poor wear under heavy duty conditions and at higher friction levels |
Heat Treatment |
Inhouse Heat treatment process |
Outsourced in most of the factories |
Grain alignment to give better raw material strength and to reduce internal stress |
Testing
We rigorously test the product post production to ensure it exceeds the highest quality standards.
- Measurement and materials testing to determine whether the crank is as per specification.
- Testing is done via our in-house dyno- facility and compared against the OE benchmarks
Parameter |
Details |
At RITSUKA |
Chinese Product |
RITSUKA Advantage |
Testing Standards |
Incoming Parts |
100% Inspection & Testing |
Random / No Testing |
Minimal chances of In-house rejection levels pre-finished / finished product |
In process |
Inhouse facility includes
- Material composition test
- Random Dimensional check with Three axis coordinate measuring machine
|
- Visual testing
- On demand testing from external agencies
|
- Controlled Standard Parameters at every Process
- Three axis coordinate measuring machine
- 0.002mm ~ 0.003mm tolerance range is maintained
|
Final Inspection |
Fitment check using pneumatic gauge, Hydraulic / Electronic Universal testing machines |
Manual inspection |
Ensures safe operation and adequate durability We have both Electronic and Hydraulic universal testing machine (UTM) for testing the tensile strength and compressive strength of materials used in manufacturing |
Precision
We ensure high standards of reliability, safety and service life. Our commitment to quality, from research and development through the entire production process to logistics and customer service, has been approved by quality management audit. The perfection we achieve is the result of consistent precision that we live by at every stage of our production.
CONNECTING ROD TEST REPORT |
Part |
5D9 Con Rod |
Sample Qty |
2 |
Manufacturer |
RITSUKA |
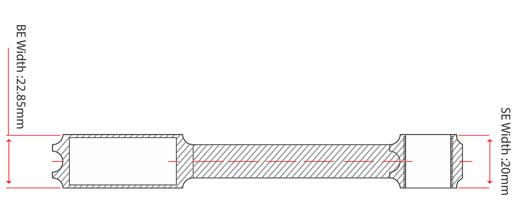 |
S.no. |
Technical Requirement |
Standard |
Test Method |
Detection Result |
Conclusion |
1 |
Appearance Check |
— |
Visual |
OK |
OK |
2 |
Small Head thickness |
±0.05 |
Micrometer |
-0.002 |
OK |
3 |
Small hold roughness |
0.4 MAX |
Roughness Instrument |
0.24 |
OK |
4 |
Aperture of small hole |
Ø13±0.25 |
Air momentum meter |
0.19 |
OK |
5 |
Orifice roundness |
0.003 |
Air momentum meter |
0.026 |
OK |
6 |
Pinhold cylindercity |
0.003 |
Air momentum meter |
0.017 |
OK |
7 |
Big hold roughness |
0.2 MAX |
Roughness Instrument |
0.14 |
OK |
8 |
Aperture of Big hole |
Ø35±0.04 |
Air momentum meter |
0.007 |
OK |
9 |
Macropore Cylindercity |
0.003 |
Air momentum meter |
0.018 |
OK |
10 |
Thickness of large head |
14±0.05 |
Air momentum meter |
0.024 |
OK |
11 |
Centre distance |
3.5±0.05 |
VernierCaliper |
-0.002 |
OK |
12 |
Carbon Depth |
0.8-1.1mm |
Microscope |
0.86 |
OK |
13 |
Surface Hardness |
59-63HRC |
Micro hardness tester |
59.5 |
OK |
14 |
Core Hardness |
28-43HRC |
Micro hardness tester |
34 |
OK |