Raw Material
Our lights and light parts are manufactured of high grade raw material of ABS (PA-709) – Acrylonitrile Butadiene Styrene (ABS).
ABS combine the strength and rigidity of acrylonitrile and styrene polymers with the toughness of polybutadiene rubber. While the cost of producing ABS is roughly twice the cost of producing polystyrene, it is considered superior for its hardness, gloss, toughness and electrical insulation properties. ABS also have a strong resistance to corrosive chemicals and /or physical impacts. It is very easy to machine, light-weight and has a low melting temperature making it particularly simple to use in injection moulding processes. Metal coating has excellent adhesion to ABS.
S.no. |
Parameter |
Details |
RITSUKA |
Chinese Product |
RITSUKA Advantage |
1 |
Child Parts |
Connector |
Inhouse |
Outsource |
- Better quality control over inhouse produced parts
|
Wire |
Outsource |
Outsource |
|
Bulb |
Inhouse |
Outsource |
- Better quality control over inhouse produced parts
|
2 |
Raw material |
Outer body |
ABS/PP |
Recycled PP (80/ 20) |
- Excellent impact strength
- Strong adhesion to powder coating.
|
Lens |
PC/Glass |
Glass |
- Light material
- Better Transparency
|
Polypropylene (PP)
We also utilize another very beneficial raw material of Polypropylene (PP). Polypropylene is a very useful plastic for injection molding. Polypropylene is easy to mold despite its semi-crystalline nature, and it flows very well because of its low melt viscosity. This property significantly enhances the rate at which you can fill up a mold with the material. Shrinkage in polypropylene is about 1-2% but can vary based on several factors, including holding pressure, holding time, melt temperature, mold wall thickness, mold temperature, and the percentage and type of additives.
Polycarbonate (PC)
Polycarbonate (PC) plastics are a naturally transparent amorphous thermoplastic. Although they are made commercially available in variety of colors, the raw material allows for the internal transmission of light nearly in the same capacity as glass. Polycarbonate is an incredibly useful plastic for applications requiring transparency and high impact resistance. It is lighter alternative to glass and a natural UV filter, so it is often used in light diffuser and lens for light parts. Polycarbonate also has a very good heat resistance and can be combined with flame retardant materials without significant material degradation. Polycarbonate plastics are engineering plastics in the sense that they are typically used for more capable, robust materials such as an impact resistant glass like surfaces.
Manufacturing
Our standardized machinery and excellent technical expertise help us to manufacture high quality spare parts. Our factory has its own in-house mould shop to rectify and develop new moulds. After the processes of injection moulding and painting, all the light parts are assembled, and quality checked further.
Parameter |
Details |
RITSUKA |
Chinese Product |
RITSUKA Advantage |
Manufacturing Process |
Injection moulding |
Inhouse automatic machine |
Outsourced |
Inhouse manufacturing ensures better quality control on produced parts |
Powder coating |
Inhouse automatic machine |
Manual coating |
Inhouse manufacturing ensures better quality control on produced parts |
Assembly |
Inhouse |
Inhouse |
Inhouse manufacturing ensures better quality control on produced parts |
Testing
All our lights and light parts are tested on international standards and 100% quality inspection of each part during production enables us to attain zero defects and utmost precision.
Photometry
Photometric globe is used to check all the electrical parameters of the bulb such as voltage, wattage, current, lumens and color temperature (CCT)
Parameter |
Details |
RITSUKA |
Chinese Product |
RITSUKA Advantage |
Testing Standard |
Incoming Quality Inspection |
100% inspection of incoming parts |
No testing |
This ensures that produced parts are within tolerance limit as per Acceptance Quality Limit (AQL) |
In process |
100% quality check at different processes |
No quality check, since it requires extra manpower/extra cost |
This ensures that produced parts are within tolerance limit as per AQL |
Final inspection |
All the products are checked before dispatch to ensure good quality |
No quality check, since it requires extra manpower/extra cost |
Defect free product to customer. |
The following diagram shows the relative impact strength of polycarbonate when compared to the impact strength of other commonly used plastics such as ABS, PS or nylon.
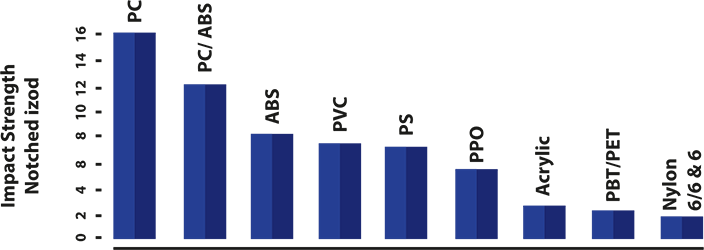
-
Paint Adhesion Test
A crosshatch pattern is made through the film to the substrate. Detached flakes of coating are removed by brushing with a soft brush. Pressure-sensitive tape is applied over the crosshatch cut. Tape is smoothed into place by using a pencil eraser over the area of the incisions. Tape is removed by pulling it off rapidly back over itself as close to an angle of 180°. Adhesion is assessed on a 0 to 5 scale. [0- Greater than 65% area removed & 5 is 0% area removed]
Parameter |
Details |
RITSUKA |
Chinese Product |
RITSUKA Advantage |
Testing Standard |
Paint adhesion test |
In-house testing |
No testing |
All the tests are performed as per GB standard to ensure defect free product |
-
Tensile Strength Test
The sample is molded into a dog bone shaped tensile bar which is gripped on both ends using a tensile tester. The tensile tester pulls on the bar at a constant speed until it breaks into two pieces. The force on the brand how much the bar stretches is continuously measured during the test. Tensile strength (stress) is calculated by dividing the maximum load by the original cross-sectional area of the test bar stretched by the original length of the bar.
Parameter |
Details |
RITSUKA |
Chinese Product |
RITSUKA Advantage |
Testing Standard |
Tensile Strength |
In-house testing |
No Testing |
All the tests are performed as per GB standard to ensure defect free product |
-
Vibration Test
Lights are tested to check the quality of the product on erratic/irregular roads
Parameter |
Details |
RITSUKA |
Chinese Product |
RITSUKA Advantage |
Testing Standard |
Vibration test |
In-house testing |
No Testing |
All the tests are performed as per GB standard to ensure defect free product |